Emerald Virtuo Custom Guitar
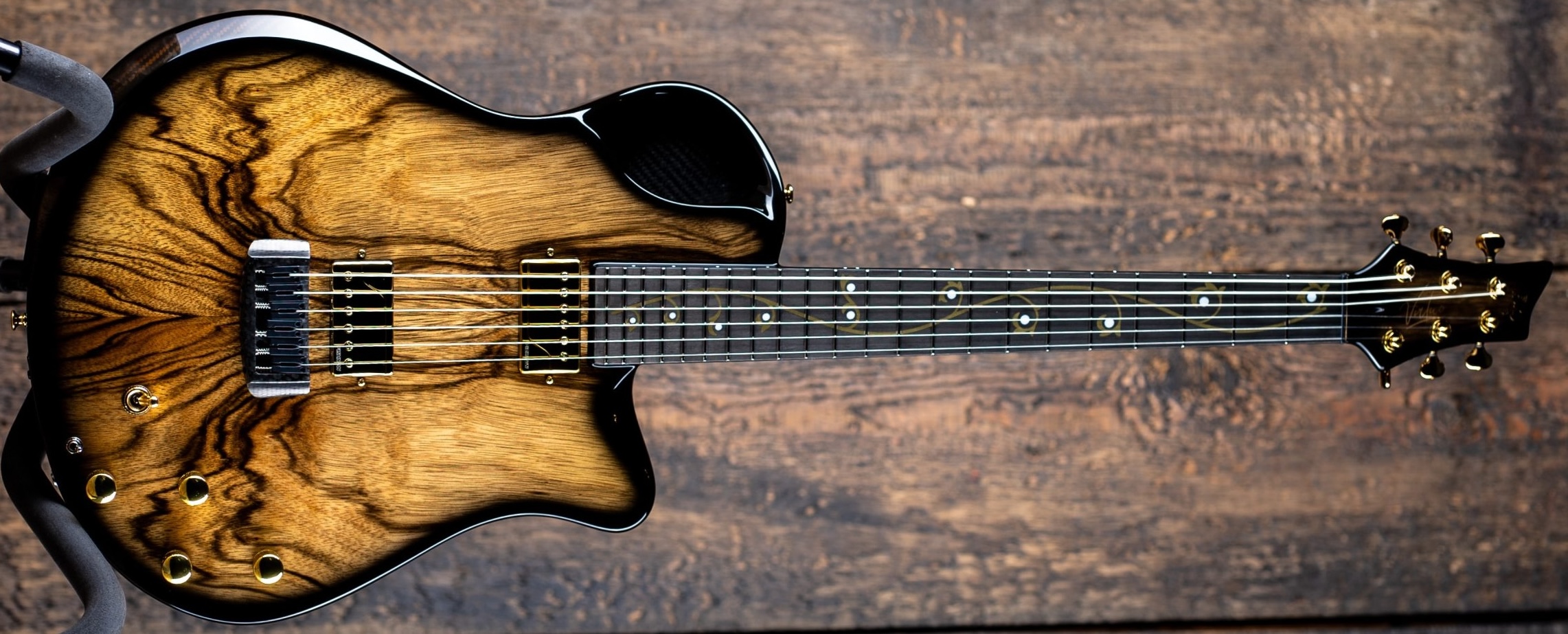
Introduction
I am now the proud owner of this fantastic custom guitar - it is so good, that I decided to dedicate an entire page to it.
This guitar has so many plus points and is, to me, the perfect studio guitar.
It is an acoustic, electric, and MIDI ready guitar with a huge number of potential sound combinations.
Construction and manufacture
The main guitar and neck is constructed from one piece of F1 grade moulded carbon fibre with a separate piece of uni-directional carbon fibre for the fretboard, which is bonded on later.
The body, once in the mould, is infused with resin and put in an oven to cure and harden. The result is an extremely strong, resilient, and lightweight guitar.
My design included a wood veneer that is bonded to the top surface of the guitar and headstock. Its position corresponds exactly to where your design dictated in the 3D Builder.
The fretboard is then prepared and bonded onto the neck. Stainless steel frets are used.
The next is a long painting and polishing process. Finishing to an extremely high standard is one of Emerald's great strengths - I've never seen a mediocre finish on one of their guitars - they all look great. Apparently, they are also open to doing custom paint jobs with artwork and the like, which is cool.
The bridge is then bonded to the body. The bridge is also made of a single piece of machined carbon fibre. In the case of the Virtuo, this also contains 6 individual GraphTech piezo ghost pickups; resulting in one pickup per string - these individual outputs are used for the MIDI output and combined for the acoustic output.
Every guitar then goes through a PLEKing process. PLEK machines are sophisticated (and expensive) machines that can cut nuts and grind frets under computer assisted control. First the guitar is scanned with its neck under string tension, the analysis from this then determines each fret's ideal profile and the machine can then grind them appropriately. This results in an extremely accurate fretboard profile.
Next, the electronics are fitted and tested, followed by final setup.
Every custom guitar is the photographed and added to the Emerald website gallery, along with its serial number (a great idea, in my opinion).
Usually, every custom guitar is featured every Friday on the company's YouTube channel's shipping video (another nice/clever touch).
Offset Soundhole
All of Emerald's acoustic guitars use a quite unique soundhole. As you can see, the soundhole projects the sound upward toward the player as well as outward toward an audience or microphone.
Another advantage to this approach is that it allows the guitar's top/front to be allowed to resonate without being compromised. Also, the sound isn't projected directly out to the strings, making unplayed strings resonate as much as a standrd acoustic would.
Truss rod
Why do you need a truss rod in something that is so stable as a carbon fibre construction? Well, they include a double action truss rods so that the neck can be adjusted for relief, depending on the string gauge being used, because the PLEK process only takes into account the relief for the tension of the strings that are supplied as standard.
Stability
If you look at the Emerald range of guitars, you will see that they include all manner of designs that would be difficult, if no impossible to make using wood. The stability and strength of carbon fibre allows them to build acoustic twin-neck guitars, harp guitars, acoustic basses, etc. that don't move with changing humidity and temperatures. I have owned a number of acoustic guitars in my time and I've always had problems with ever-moving neck actions and tuning problems - this is where carbon fibre comes to the rescue.
Comfort and Access
Being able to mould the guitar as a single piece means that they can design guitar bodies that are impossible otherwise. They make the most of this with their ergonomic body shapes that fit the contour of your body instead the hard edges that you find on all-wood acoustics.
With the neck being part of the whole, instead of being added separately, means that the neck can remain thin all the way past the start of the body. No more heels getting in the way!
Pickups
The Virtuo has two main pickup systems:
Fishman Fluency pickups
These pickups are active pickups that offer three different voices. These are:
- Modern active high output hum bucker
- Modern passive attack high output hum bucker
- Bright tone single coil
Each voice is selectable via push/pull controls - see further info below.
GraphTech Ghost Piezo pickups
These pickups are responsible for both the acoustic output and MIDI output and are situated in the bridge. Each string has its own pickup which are sent individually to the MIDI output, and combined for the acoustic output.
Controls
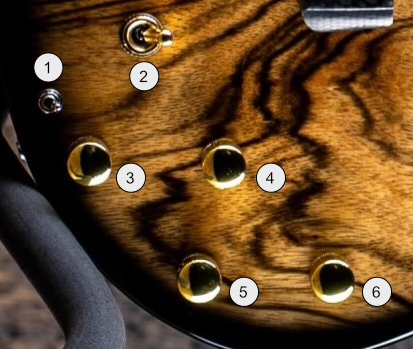
- Pickup type selector. This is a 3-way switch that lets you select either or both the acoustic GraphTech pickups and/or the electric Fishman Fluence pickups.
- The Fishman Fluence selector switch. Selects between the bridge and neck pickups or both in the central position.
- Tone control for the Fishman pickups + Push/pull to switch between vintage and modern hum buckers.
- Volume control for the Fishman pickups + Push/pull to switch between hum bucker and single coil.
- MIDI output volume.
- GraphTech ghost piezo volume + Push/pull to switch between alternative voicing.
As you can see above, all rotary pots, apart from MIDI volume, have a second function if they are pulled up.
Outputs
There are 2 output sockets.
13-pin MIDI socket
This socket takes the 6 individual signals from the piezo saddle pickups and outputs them via this socket.
This output can then be used with a compatible MIDI expander such as a Roland GR-55, Boss SY-100, etc.
Note that there is a tiny slider switch under this socket. This is for compatibility with different converter brands. The left position is for Roland/Boss and the right position is for Axon. For other manufacturers, you will have to experiment between the two.
1/4 inch jack
If you use a standard mono cable, the acoustic and electric outputs are mixed, as you would expect.
However, you can also use a stereo 1/4 inch cable to split off the outputs of the acoustic and electric. This would be very useful in a live situation where the electric output goes to, say, a high gain amp but the acoustic output goes to a PA or other amplifier or you could record both outputs at the same time to two channels of a DAW etc..
Strings
The Virtuo is shipped with electric strings unless you request otherwise. As it is both an acoustic and electric guitar, certain considerations are to be made. It can, of course be stung with acoustic strings but if this is the case, the acoustic strings should have a high magnetic content in order to allow the Fishman Fluence pickups to work to their best.
The electric strings used also have a light top but heavy bottom. The heavier bottom strings apparently help the acoustic response of the guitar (it is, after all, both and acoustic and an electric guitar).
- Electric string gauge is 10-52
- Acoustic strings - NewTone double wound strings - for extra magnetism
The following video gives you detailed information on strings and general setup information for the Virtuo:
Designing your guitar
Although you can buy one of their in-stock guitars off the Emerald website, the most fun comes from designing your own using the online 3D builder.
The 3D builder allows you to choose the type and colour of carbon fibre you want, gives you an extensive choice of wood veneers to choose from, the hardware colour, and extensive fretboard inlay options.
Choosing a veneer is one of the most fun things to do. Here you can choose from an extensive range of hard woods that have been scanned in at high resolution. You can fine-position them, flip them 180 degrees (which I recommend as you can get some surprising differences), and even opt for a transparent colour or burst with some woods.
You can also save your designs and get a return URL to tweak further if you like. I ended up with about 8 tabs open in my browser before deciding on the design I wanted to go with.
Try it yourself - it's fun!
The order process
Once you have decided on your design you can simply go through to the purchase screen. Alternatively, you can contact the company and talk about other options such as custom art work or alternative finishes etc. A serial number was also assigned.
I went straight to the order page and paid with no problem.
Emerald gave me an approximate lead time for the build of 2 months.
I received email updates along the way as follows:
- Day 1 - Receipt with a picture of my design and a Welcome to Emerald email allowing me to create an account.
- Day 10 - An update email to inform me that my guitar had made it to the top of the production schedule and was being moulded etc.
- Day 43 - An update to inform me that it had passed through the painting and polishing process and was headed for final setup.
- Day 51 - An update to inform me that my guitar was complete and ready to ship and that it will be featured on the upcoming shipping video.
- Day 53 - Received my guitar!
- Day 61 - Featured in the weekly shipping video.
The shipping video that featured my guitar was delayed because of a combination of Black Friday deals going on and the fact that it was the Emerald owner's birthday. Otherwise it would probably have been viewed beforehand.
Here it is being featured: